DESIGN: HYPERBARIC FACILITIESRecord of Changes - 4_159_010002FOREWORD - 4_159_010003CONTENTS - 4_159_010004CHAPTER 1. INTRODUCTION - 4_159_010005APPENDIX A. DESIGN MANUAL 39 HYPERBARIC FACILITIESCCB Application Notes - 4_159_010007HYPERBARIC FACILITIES DESIGN MANUAL 39CONTRIBUTORSFOREWORD - 4_159_010014CONTENTS - 4_159_010015CONTENTS-continued - 4_159_010016CONTENTS-continued - 4_159_010017CONTENTS-continued - 4_159_010018CONTENTS-continued - 4_159_010019CONTENTS-continued - 4_159_010020CONTENTS-continued - 4_159_010021CONTENTS-continued - 4_159_010022CONTENTS-continued - 4_159_010023CONTENTS-continued - 4_159_010024CONTENTS-continued - 4_159_010025CONTENTS-continued - 4_159_010026CONTENTS-continued - 4_159_010027CONTENTS-continued - 4_159_010028CONTENTS-continued - 4_159_010029CONTENTS-continued - 4_159_010030CONTENTS-continued - 4_159_010031Figures - 4_159_010032Figures-continued - 4_159_010033Figures-continued - 4_159_010034Figures-continued - 4_159_010035Tables - 4_159_010036CHAPTER 1. HYPERBARIC FACILITIESPERSONNEL SAFETYCHAPTER 2. HYPERBARIC PRESSURE VESSELSDESIGN CONSIDERATIONS-continuedMANUFACTURER'S DESIGN REPORTUSER'S DESIGN SPECIFICATION-continuedSection 2. MATERIALS FOR HYPERBARIC VESSELSPRESSURE HULL/VESSEL MATERIALSBOLTING MATERIALCLASS 2, Material of known propertiesCLASS 3, Materials whose properties are to be provenMATERIALS PERMITTEDMATERIAL TOUGHNESSFigure 2-1. Typical Charpy Test Data on High Strength SteelsFigure 2-2. Typical NDT Specimen Performance at Different Temperatures when Tested to ASTM A-208Figure 2-3. Typical Charpy V Impact Test DataFigure 2-4. Crack Arrest Curve Overlayed to Demonstrate the Residual Stress Pattern Associated With WeldmentFigure 2-5. Toughness Relative to Direction of Rolling and Effect of Rolling Ratio of High Strength SteelsFigure 2-6. Toughness Relative to Direction of Rolling of Aluminum Alloy PlatesCORROSION CONSIDERATIONSCORROSION CONSIDERATIONS-continuedSection 3. DESIGNExperimental MethodsStress Intensity LimitsPrimary bending stressTable 2-1. CLASSIFICATION OF TRESSES FOR SOME TYPICAL CASESTable 2-1. CLASSIFICATION OF TRESSES FOR SOME TYPICAL CASES-continued - 4_159_010063Table 2-1. CLASSIFICATION OF TRESSES FOR SOME TYPICAL CASES-continued - 4_159_010064The amplitude of alternating stress intensityFigure 2-7. Stress Categories and Limits of Stress IntensityA hyperbaric vesselFigure 2-8. Fatigue Design Curve for Low Carbon and Alloy SteelsNOTE - 4_159_010069DESIGN REQUIREMENTS - 4_159_010070Table 2-2. STRESS INTENSITY k FACTORS FOR VARIOUS LOAD COMBINATIONSAD-160.1, "Operating ExperienceArticle D-5, "Openings and Their Reinforcement."APPENDIX 3, "RULES FOR BOLTED FLANGE CONNECTIONS."APPENDIX 6, "EXPERIMENTAL STRESS ANALYSIS-continuedEXAMPLE OF DESIGN BY ANALYSIS AS APPLIED TO A SPHERICAL CHAMBERFigure 2-9. Schematic of Proposed Class 1 VesselMaterials and Initial CalculationsSupport Skirt Compressive StressNOTE - 4_159_010080Penetrations & Openings, ReinforcementPenetrations & Openings, Reinforcement-continuedInlet and Outlet Nozzles - 4_159_010083Inlet and Outlet Nozzles-continuedNote - 4_159_010085Figure 2-10. Details of Reinforcement for 4.0-Inch NozzleThe inner corner radiusViewport Mounting RingFigure 2-11. Details of Window ReinforcementDoorFigure 2-12. Details of Reinforcement for 40.0-Inch-Diameter PenetrationDesign of the flangeFigure 2-13. Details of Entranceway and DoorStress AnalysisMethod of AnalysisFigure 2-14. Model No.1 for Input to Computer ProgramFigure 2-15. Model No. 2 for input to Computer ProgramFigure 2-16. Model no. 3 for Input to Computer ProgramModel No. 2Figure 2-17. Details of 4.0-Inch Nozzle From Model No. 1Figure 2-18. Some Maximum Stresses in Model No. 1Categorization of Stress - 4_159_010102Figure 2-19. Details of Geometric Model of the 40.0-Inch Entranceway ReinforcementFigure 2-20. Some Maximum Stresses in Model No. 2Figure 2-21. Some Maximum Stresses in Model No. 3SIGMA PHI STRESSESStress IntensitiesStress Intensities-continued - 4_159_010108Stress Intensities-continued - 4_159_010109Stress Intensities-continued - 4_159_010110Table 2-3. Maximum Stress Intensities in Model No. 1Table 2-4. Maximum Stress Intensities in Model No. 2Table 2-5. Maximum Stress Intensities in Model No. 3Stress Index MethodDesign ChangesMiscellaneous ConsiderationsEXAMPLE OF DESIGN BY ANALYSIS AS APPLIED TO A CYLINDRICAL CHAMBERMinimum Shell ThicknessInlet and Outlet Nozzles - 4_159_010119Entranceway-continuedFigure 2-22. Configuration of 5.0-Inch Diameter Inlet and Outlet NozzlesFigure 2-23. Detail of Shell, Viewport Penetration in Head and EntrancewayHatchSupports - 4_159_010124Figure 2-24. Front View of Cylindrical ChamberMethod of Analysis-Symmetric ProblemsMethod of Analysis-Symmetric Problems-continuedFigure 2-27. Details of Viewport Penetration Reinforcement in CylinderMethods of Analysis-Nonsymmetric ProblemsMethods of Analysis-Nonsymmetric Problems-continuedFigure 2-29. Circumferential Stress in Vessel at Hatch EndFigure 2-30. Meridional Stresses in Vessel at Hatch EndFigure 2-31. Computer Model and Stress Ouput for Hatch CoverCategorization of Stress - 4_159_010134Figure 2-32. Three Component Model of Viewport Penetration in Cylinder for Input to ComputerFigure 2-33. Hoop Stresses in Vicinity of Viewport Penetration in CylinderStress Intensities-continued - 4_159_010137REFERENCES - 4_159_010138REFERENCES-continued - 4_159_010139CHAPTER 3. APPURTENANCESFigure 3-1. Flat Plate ViewportFigure 3-3. Double Conical Frustum WindowFigure 3-5. Flat Window Pressure Sealing With Exterior BoltingMATERIAL SELECTION - 4_159_010144Figure 3-7. Commercially Available Glass WindowsFIELD OF VIEW CONSIDERATIONSFigure 3-8. Refractive Effect of Flat WindowFigure 3-9. Limiting Aperture Locations on Various Viewport ConfigurationsFigure 3-10. Graphical Determination of Monocular and Binocular Viewing Fields in the Horizontal PlanePhysical PropertiesTable 3-1. Specified Values of Physical Properties for Each LotNote 1-continuedTable 3-2. Specified Values of Physical Properties for Each CastingWINDOW DESIGN - 4_159_010154Figure 3-11. Standard Window GeometricsSTCP of an acrylic plastic window Figure 3-12. Short Term Critical Pressure of Flat Disc Acrylic Windows to 7,250 psiFigure 3-13. Short Term Critical Pressure of Flat Disc Acrylic Windows to 43,500 psiFigure 3-14. Short Term Critical Pressure of Conical Frustum Acrylic Windows to 7,250 psiFigure 3-15. Short Term Critical Pressure of Conical Frustum Acrylic Windows to 43,500 psiTable 3-3. Conversion Factors for Acrylic Plastic Flat Disc WindowsTable 3-4. Conversion Factors for Acrylic MasticTable 3-5. Conical Frustum Windows for Design Pressures in Excess of 10,000 psi For flat disc windowsWINDOW SEATSFigure 3-16. Seat Cavity Requirements (Conical Frustum, Spherical Shell, and Flat Disc)Figure 3-17. Seat Cavity Requirements (Double Beveled Disc)WINDOW SEALSDIMENSIONAL TOLERANCES AND SURFACE FINISH-continuedFABRICATION OF WINDOWSTable 3-6. Annealing Schedule for Acrylic Plastic WindowsPRESSURE TESTING OF WINDOWSSection 2. DOORS AND CLOSURESFigure 3-18. Typical Recompression Chamber DoorFigure 3-19. Typical Service LockTable 3-7. Standing Anatomical DimensionsTable 3-8. Seated Anatomical DimensionsFigure 3-20. Typical Recompression Chamber EntranceCLOSING MECHANISMSFigure 3-21. Breach LockFigure 3-22. Spring ClampsFigure 3-23. Segmented Ring ClosureFigure 3-24. Swing Bolt ClosureFigure 3-25. Clamping Bar ClosureDOOR AND CLOSURE HINGESFigure 3-26. Compound HingesFigure 3-27. Conventional Gasketed ClosureThe threaded cap closure seal Figure 3-29. Threaded Cap ClosureFigure 3-30. Threaded Plug ClosureFigure 3-31. Flat Face O-Ring Seal Suitable for High PressureFigure 3-32. Floating Ring Seal for High PressuresFigure 3-33. O-Ring Sealed Penetrator PlugDOOR AND CLOSURE LOCATIONFigure 3-34. Chamber Door with O-Ring in Dovetail GrooveSection 3. INTERIOR APPURTENANCESREFERENCES - 4_159_010197CHAPTER 4 FOUNDATIONSSECTION 1. SITE SELECTIONSECTION 2. SUBSURFACE EVALUATIONLABORATORY TESTSSECTION 3. FOUNDATION ANALYSIS AND DESIGNFOUNDATION TYPESFOUNDATION TYPE SELECTIONSECTION 4. STRUCTURAL SUPPORTSDESIGN PARAMETERS PECULIAR TO EACH MATERIALReinforced Concrete-continuedSECTION 5. INSTALLATION IN EXISTING BUILDINGSFOUNDATION TYPES-continuedSTRUCTURAL SUPPORTSREFERENCES - 4_159_010211CHAPTER 5. PIPINGTable 5-1. Hyperbaric Facilities - Applicable Codes, Specifications, and StandardsSECTION 2. DESIGN CONSIDERATIONSPROCEDURES-continuedSection 3. PIPING SYSTEM MATERIALSTable 5-2. Class 1 Piping MaterialsJustification of Class 3 MaterialsMATERIAL COMPATIBILITYCompatibility with OxygenTable 5-3. Oxygen Systems Contained in MIL-STD-777ENGINEERING PROPERTIESSection 4. CONSTRUCTION CONSIDERATIONSTable 5-4. Wall Thickness for BendingPIPE JOINTSBrazing Qualification-continuedFlanged Joints/Bolted FlangesSection 5. DESIGN GUIDANCEFluid Flow ApproximationsFriction factor-continuedFigure 5-1. Friction Factors for Clean Commercial Steel and Wrought Iron PipeEquivalent pipe lengthFigure 5-2. Resistance of Valves and FittingsTable 5-5. Physical Properties of GasesTable 5-6. Reasonable Velocities for the Flow of Water Through PipeTable 5-9. Flow of Water Through Schedule 40 Steel PipeTable 5-10. Flow of Air Through Schedule 40 Steel PipeTable 5-11. Commercial Wrought Steel Pipe DataTable 5-11. Commercial Wrought Steel Pipe Data-continuedThe total pressure dropApproximation for Water, Low FlowApproximation for Oxygen, Low FlowApproximation for Helium, High FlowTable 5-12. Typical Dimensions for Commercially Available TubingDESIGN FOR PRESSUREMinimum Wall Thickness, Straight Pipe Under Internal PressureSYSTEM DETAILING AND FINAL FLOW ANALYSISFinal Routing of Pipe and Selection of Supports and AnchorsPipe Joint SealsSTRUCTURAL ANALYSISStructural Design Specification-continuedAnalysis Procedure for Category I and II Piping SystemCategory III and IV Piping SystemsNOISE CONSIDERATIONSAcceptable Noise LevelsNoise ControlCOLOR CODE FOR PIPING SYSTEMSREFERENCES - 4_159_010258REFERENCES-continued - 4_159_010259CHAPTER 6. LIFE SUPPORT SYSTEMSFigure 6-1. Percentage of Oxygen in Breathing Mixture as a Function of Depth and Oxygen Partial PressureOxygen versus Depth RangesContaminantsFigure 6-2. Limiting Percent of CO2 in Breathing Gas Mixture as a Function of Depth and CO2 Partial PressureWater VaporFigure 6-4. Linmiting Percent CO in Breathing Mixture as a Function of Depth and CO Partial PressureBREATHING GAS CONSUMPTION REQUIREMENTSFigure 6-5. Total Hydrocarbons Allowed Vs. Dive DepthFigure 6-7. Allowable Sulfur Dioxide Vs. Dive DepthTEMPERATURE-HUMIDITY REQUIREMENTSPRESSURIZATION/DEPRESSURIZATIONSTORAGE FLASKSPREVENTION OF LINE FREEZEFigure 6-11. Horizontal Storage FlaskSection 3. GAS SYSTEMSGAS MIXINGCARBON DIOXIDE CONTROLFigure 6-16. Carbon Dioxide ControlFigure 6-17. Characteristics of Three Carbon Dioxide AbsorbentsTEMPERATURE-HUMIDITY CONTROLFigure 6-18. Relation of Pressure Drop to Superficial Velocity, Pressure, and Bed DepthsHeating and cooling coils-continuedPsychrometric CalculationsPsychrometric Calculations-continuedFigure 6-20. Temperature-Humidity ControlFigure 6-21. Psychrometric Chart 1- Data for Gas Mixtures at Pressures From 14-7 Psia to 200 PsiaFigure 6-22. Psycrometric Chart 2 - Data for Gas Mixtures at Pressures From 100 Psia to 600 PsiaFigure 6-23. Psychrometric Chart 3 - Correction for Enthalpy of Moisture ContentGAS DISTRIBUTIONCOMPRESSORS/TRANSFER PUMPSSection 4. AUXILIARY BREATHING SYSTEMSSection 5. ATMOSPHERE MONITORINGFigure 6-26. Typical On-Line Gas Analysis SystemSection 7. POTABLE WATER AND SANITARY SYSTEMFigure 6-27. Typical Potable Water and Sanitary SystemFigure 6-28. Typical Sanitary System InterlockLiquid Level IndicatorsREFERENCES - 4_159_010298CHAPTER 7. WET CHAMBER WATER SYSTEMSFigure 7-1. Wet Pot Water System Schematic DiagramLINESSection 2. WATER TREATMENTSection 3. WATER TEMPERATURE CONTROLFigure 7-2. Viewport Insulating CoverREFERENCES - 4_159_010305CHAPTER 8. FIRE PROTECTION AND EXTINGUISHING SYSTEMSManual ActivationFigure 8-1. Pressurized Tank for Fire ExtinguishingFIRE EXTINGUISHERSOxygen-continuedAtmosphereFigure 8-2. Physiologically Usable, Fire-Safe Region for Helium-Oxygen AtmospheresFigure 8-3. Combustibility of Material in a Chamber Pressurized First with Air, then with HeliumSTRUCTURAL - 4_159_010314EMERGENCY BREATHING APPARATUSREFERENCES - 4_159_010316CHAPTER 9. ELECTRICAL SYSTEMSSection 2. POWER SUPPLYACCEPTABLE POWER SUPPLYSection 3. WIRINGExplosion-Proof CircuitsFigure 9-2. Example of an Energy-Limited SupplyGROUNDING - 4_159_010323Figure 9-3. Hull Mounted Submarine Navigation LightFigure 9-4. Light Pipe Pressure Containing WindowFigure 9-6. Hull Mounted Submarine Navigation Light Replacement by Light Pipe Pressure Containing WindowFigure 9-8. External Light Heat Shield and DissipationPERSONNEL LIGHTING REQUIREMENTSREFERENCES - 4_159_010329CHAPTER 10. COMMUNICATION SYSTEMSINTERCOM POWER REQUIREMENTSFigure 10-1. Fundamental Lengthwise Resonant Frequencies for Various Closed Chamber Lengths and PressuresSection 2. VIDEO COMMUNICATIONSFigure 10-2. Example of Audio SystemCAMERA STYLES AND SELECTIONLIGHTING REQUIREMENTSCHAPTER 11. CHAMBER OPERATING CONTROL SYSTEMSFigure 11-2. Suggested Parameters for Mockup of Standing Operator WorkplacesSection 2. CONTROL PANEL DESIGNREFERENCES - 4_159_010340CHAPTER 12. LUBRICANTS, SEALANTS, AND CLEANING PROCEDURES FOR HYPERBARIC SYSTEMSTable 12-1. Lubricants-OilsTable 12-3. Lubricants-Dry FilmsTable 12-5. Thread Sealants and LubricantsTable 12-6. Adhesives, Plastics and ElastomersSection 2. CLEANING PROCEDURETable 12-8. Limits for Atmospheric ConstituentsTable 12-9. Maximum Concentration for Some Common Contaminants in Saturation Complex AtmospheresTable 12-9. Maximum Concentration for Some Common Contaminants in Saturation Complex Atmospheres-continuedPIPING AND GAS STORAGE SYSTEMSACCEPTABLE CLEANING AGENTSREFERENCES - 4_159_010352INDEX - 4_159_010353INDEX-continued - 4_159_010354INDEX-continued - 4_159_010355INDEX-continued - 4_159_010356INDEX-continued - 4_159_0103574_159_01
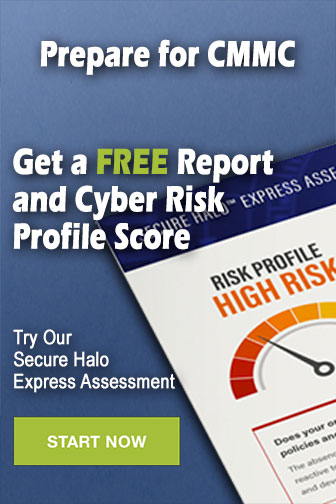